measurement and prediction of residual stresses in thick-section steel welds|Measurement and prediction of residual stresses in thick : wholesalers The Deep Hole Technique for measuring residual stresses in thick section components is used to determine distributions of residual stresses, through the thickness, of a . Matriz: ACADEMIA OS GAVIOES DO KARATE LTDA - CNPJ: 53.102.695/0001-89 - Av. Emílio Ribas, 3143 - Vila Galvão - Guarulhos - SP - 07051-001
{plog:ftitle_list}
WEB20 de nov. de 2023 · Resultado Jogo do Bicho de Outros lugares do dia 20 de Novembro de 2023. Resultado Nacional Jogo do Bicho de hoje, ontem e outras datas você encontra na Resultado Fácil, confira os principais horários da Nacional Loterias: LN 02hs, LN 08hs, LN 10hs, LN 12hs, LN 15hs LN 17hs, LN 19hs e LN 22hs. Agora você pode consultar os .
Significant levels of residual stress are developed in the production of thick-section steel welds. Residual stress can be measured by a variety of methods, although few offer the . Residual stress can be measured by a variety of methods, although few offer the ability to determine the spatial distribution completely through the thickness. This paper . The Deep Hole Technique for measuring residual stresses in thick section components is used to determine distributions of residual stresses, through the thickness, of a . The purpose of the present study was to obtain detailed measurements and predictions of residual stresses in thick-section components containing electron beam .
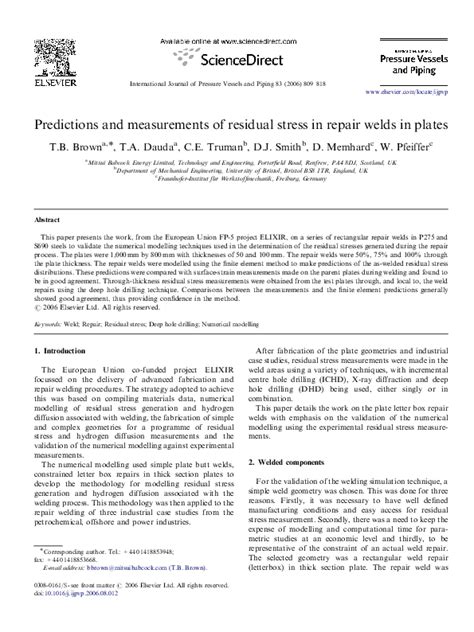
The numerical modelling used simple plate butt welds, constrained letter box repairs in thick section plates to develop the methodology for modelling residual stress generation .Measurement and prediction of residual stresses in thick-section steel welds. Journal of Strain Analysis for Engineering Design, 35(4), pp. 287–305. For guidance on citations. Zubairuddin et al. (2014) have shown that maximum longitudinal residual stresses in welds of low carbon steel and ultrahigh-strength steel are as high as their yield strength of the material. Ibrahim et al. (2016) carried out FE analysis of submerged arc welding of a 28 mm thick box section made up of A 572 Grade 50 steel. They compared FE .(DOI: 10.1243/0309324001514422) Significant levels of residual stress are developed in the production of thick-section steel welds. Residual stress can be measured by a variety of methods, although few offer the ability to determine the spatial distribution completely through the thickness. This paper summarizes recent developments in the deep-hole method for .
Although there are many simulations of residual stresses in quenched steel components there is little validation of these predictions particularly when the components are large. This is not surprising bearing in mind that the application of the through thickness measurement techniques (mechanical strain relief techniques) are problematic when the . Thermal relaxation of residual stress in thick section girth welds has been quantified by both measurement and analysis. Two girth welds, joining pairs of ex-service AISI type 316H austenitic . Cross-sectional dimensions of each specimen are shown in Table 2, with the geometric parameters defined in Fig. 1.Flange and web plates were either oxy-flame- or plasma-cut: the cutting method used for each girder is shown in Table 3.Plates were joined using submerged-arc welding using Lincolnweld LA-75 electrodes with Lincolnweld 960 flux; single . The measurement and prediction of such stresses is extremely challenging for thick section welds and even more so for welds confined to narrow regions through the component thickness. Earlier work on residual stress measurement of electron beam welds has generally been confined to relatively thin samples.
Predictions and measurements of residual stress in repair welds
1. Introduction. Residual stresses have been widely discussed in scientific literature over the past decades. In a classical study, Brinksmeier et al. [1] stated that residual stresses play a key role in distortion and mechanical strength as well as chemical and/or electrical performance. Residual stresses are a result of elastic strains that develop in a component .
chosen to measure residual stresses in the pipe girth welds because they have the capability of mapping stresses through the thickness of the components. A. Neutron Diffraction Neutron diffraction has been successfully applied to characterize the through-thickness residual stress distri-bution in austenitic stainless steel pipe welds.[18] In this The maximum thickness for ferritic steel specimens’ residual stress measurements using neutron diffraction is known to be about 80 mm. This paper proposes a new neutron diffraction configuration of residual stress measurements for cases that are over 80 mm thick. The configuration utilizes a neutron beam with a wavelength of 1.55 Å diffracted from .
DOI: 10.1016/J.IJMECSCI.2005.06.011 Corpus ID: 136669004; Measurement of residual stress in thick section composite laminates using the deep-hole method @article{Bateman2005MeasurementOR, title={Measurement of residual stress in thick section composite laminates using the deep-hole method}, author={Michael Bateman and Oh . A general prescription for as-welded residual stress distributions in stainless steel pipe butt welds of arbitrary diameter and thickness,, based solely on finite element studies, is critically . The objective of this work is to measure the welding residual stress in ASTM (A-106 Gr. b) steel pipes with 4" diameter and 6 mm thickness welded manually (SMAW) in three-pass butt joint where . The stress profile displayed by the rolled sample in Fig. 4 shows a typical bent stress level [3] and the stresses in the normal direction average to zero indicating that the overall stress state can be considered to be measured correctly. The stresses in the transverse and normal directions through the centre of the weld are shown in Fig. 5.These stress levels are of .
Measurementandpredictionofresidualstressesinthick
Residual stress variations were determined through the thickness of a 70-mm-thick ferritic–austenitic dissimilar steel weld using contour method, deep hole drilling, and neutron diffraction. The result shows that significant tensile stresses were distributed distinctly along the interface between ferritic and austenitic phases. The band of the large tensile stresses was .
The measured residual stresses are compared with FE predictions. . including thick-section steel welds consisting of a welded nozzle component which was thermally aged at 550°C for 19,644 hours . Smith DJ, Bouchard PJ, George D. Measurement and prediction of residual stresses in thick-section steel welds. J Strain Analysis 2000; 35: 287–305. Crossref. of Science. Google Scholar. 6. Prime MB. Residual stress measurement by successive extension of a slot: the crack compliance method.
tensile test uts
Using high-strength steel for offshore structures with a yield stress of 500 MPa, this study evaluated the distribution characteristics of welding residual stress in the thickness direction under the influence of constrained . Measurement and prediction of residual stresses in thick-section steel welds. David J. Smith P. Bouchard D. George. Engineering, Materials Science. 2000; Significant levels of residual stress are developed in the production of thick-section steel welds. Residual stress can be measured by a variety of methods, although few offer the ability to .
Residual stress measurements in thick section welds can be challenging. . Thick section ferritic steel welds normally undergo post-weld heat treatment (PWHT) prior to entry into service. . Measurement and prediction of residual stresses in thick-section steel welds. J. Strain Anal. Eng. Des., 35 (4) (2000) .Measurement and prediction of residual stresses in thick-section steel welds. Journal of Strain Analysis for Engineering Design, 35(4), pp. 287–305. For guidance on citations see FAQs.Validated prediction of weld residual stresses in austenitic steel pipe girth welds before and after thermal ageing, part 1: Mock-up manufacture, residual stress measurements, and materials characterisation, . The residual stress measurement techniques available for thick section welds have improved . residual stress measurements made using .
Download scientific diagram | Measured residual stresses in a ferritic steel plate 108 mm thick from publication: Measurement and prediction of residual stresses in thick-section steel welds . A general prescription for as-welded residual stress distributions in stainless steel pipe butt welds of arbitrary diameter and thickness,, based solely on finite element studies, is critically . This paper presents the work, from the European Union FP-5 project ELIXIR, on a series of rectangular repair welds in P275 and S690 steels to validate the numerical modelling techniques used in the determination of the residual stresses generated during the repair process. The plates were 1,000 mm by 800 mm with thicknesses of 50 and 100 mm. The .
Measurement and prediction of residual stresses in thick
Optimising residual stress measurements and predictions in a welded benchmark specimen: a review of phase two of the NeT task group 1 single bead on plate round robin . Measurement and prediction of residual stresses in thick-section steel welds. J. Strain Anal. Eng. Des., 35 (4) (2000), pp. 287-305. View in Scopus Google Scholar [24] Thick AISI 304L stainless steel plates were welded using the gas metal arc welding process, and through-thickness residual stresses were evaluated by finite element simulation and the deep hole .
This paper describes the application of the deep-hole technique to measure residual stresses in thick welded components. Residual stresses were evaluated in three specimens with a wall thickness .
Measurement and Prediction of Through Thickness Residual
Measured and predicted residual stresses in thick section
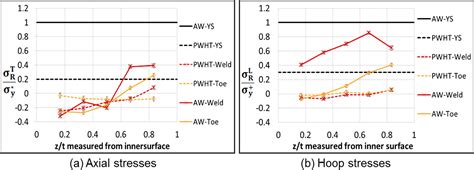
Resultado da Lá, Desastrado, Ranzinza, Smurfette, Gênio, Papai Smurf e Valente encontram refúgio com o casal vivido por Neil Patrick Harris e Jayma Mays. Assistir Os Smurfs online dublado. .
measurement and prediction of residual stresses in thick-section steel welds|Measurement and prediction of residual stresses in thick